Introducing our New State-of-the-Art Testing Facility!
Arriving at our Suffolk site THIS AUTUMN, this bespoke rig, for the testing of Swing Drive and Final Drive Hydraulic Motors, will expand our repair capabilities enormously. Specially designed for our workshop, this new equipment will enable load testing of up to 132 KW increasing the services we offer.
The total investment for this project is estimated to be around £1 million, making it the most significant investment in our 30+ year history. This substantial investment underscores our commitment to innovation and quality.
In response to increasing industry demands, we decided to invest in enhancing our testing capabilities. Our goal was to provide more comprehensive testing to ensure our products meet and exceed the expectations of our customers. This investment allows us to deliver superior quality and reliability, setting a new standard in the industry.
The highlight of our new test facility is the electronic dynamometer. This advanced tool allows us to simulate field conditions on machines and accurately measure energy usage. This capability is crucial in ensuring that every product operates to Original Equipment Manufacturer (OEM) specifications, providing our customers with unmatched confidence in the reliability of their repairs.
![1[1] Introducing our New State-of-the-Art Testing Facility!](https://plantparts.eu/wp-content/uploads/2024/06/11-300x300.png)
![3[1] Introducing our New State-of-the-Art Testing Facility!](https://plantparts.eu/wp-content/uploads/2024/06/31-1-300x300.png)
![2[1] Introducing our New State-of-the-Art Testing Facility!](https://plantparts.eu/wp-content/uploads/2024/06/21-300x300.png)
With our new facility, customers can be assured that returned repairs have undergone rigorous testing. Our facility allows us to test items more stringently than many of our competitors and even some OEM providers. This level of testing goes beyond standard batch function testing, ensuring each item performs optimally under real-world conditions.
Our test facility features a fixed, fully electronic structure with full regenerative capabilities, which are typically hydraulic. Designed for single-person operation and is fully automated, under the guidance of relevant OEMs, we are developing our own bespoke test programs and sequencing.
This unique motor test rig, distinct from a pump rig, is the only one of its kind in the aftermarket.
With this new facility, we aim to deepen our involvement in industries where we already have a strong presence, such as mining, demolition, and waste management. The ability to test large hydraulic motors and provide unmatched guarantees will allow us to offer services that other aftermarket repairers cannot.
One of the primary challenges was finding a company that could understand and meet our goals. We needed a system capable of testing a wide range of items, from 18cc to 340cc motors, with precise accuracy and data acquisition. Overcoming supply chain issues and ensuring meaningful regenerative return were also significant hurdles. Our chosen partners have demonstrated exceptional capability in addressing these needs.
We are particularly excited about the accuracy of our test results. Being one of the few suppliers in Europe to offer this level of service, we can provide industry-specific solutions with unparalleled precision.
With this advanced test facility, we are able to offer unparalleled testing services that set us apart from competitors. This investment not only strengthens our current capabilities but also paves the way for future growth and innovation.
We look forward to leveraging this facility to provide exceptional value to our customers and to continue leading the industry in quality and reliability.
We would like to invite you to see it for yourself! Simply contact the team to arrange a tour.
Our relationship with the providers has been pivotal. Collaborating directly with them, particularly a reputable Japanese firm and a UK-based team known for their bespoke projects (including the simulation of plane crashes for the entertainment industry!), has significantly improved our processes. Their problem-solving focus and commitment to innovation have been invaluable.
This project has been a collaborative effort involving various teams within our organisation. The directors’ vision, the accounts team’s diligence in managing the investment, and the technical team’s expertise in determining the necessary capacity and data accuracy were all crucial to the project’s success.
This project would not have been possible without the collective effort of our entire team. The directors, the accounts team, and the technical team all played essential roles in bringing this project to fruition. Their contributions have ensured that we now possess a comprehensive test facility that supports our growth and enhances our ability to deliver high-quality, reliable repairs.
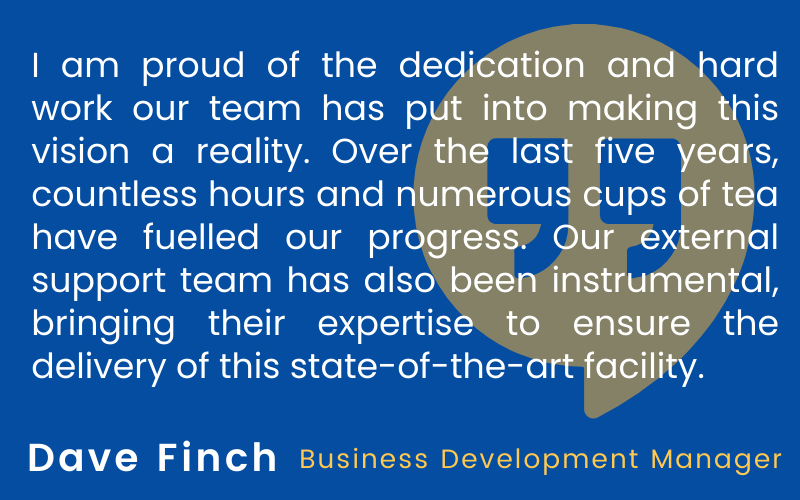